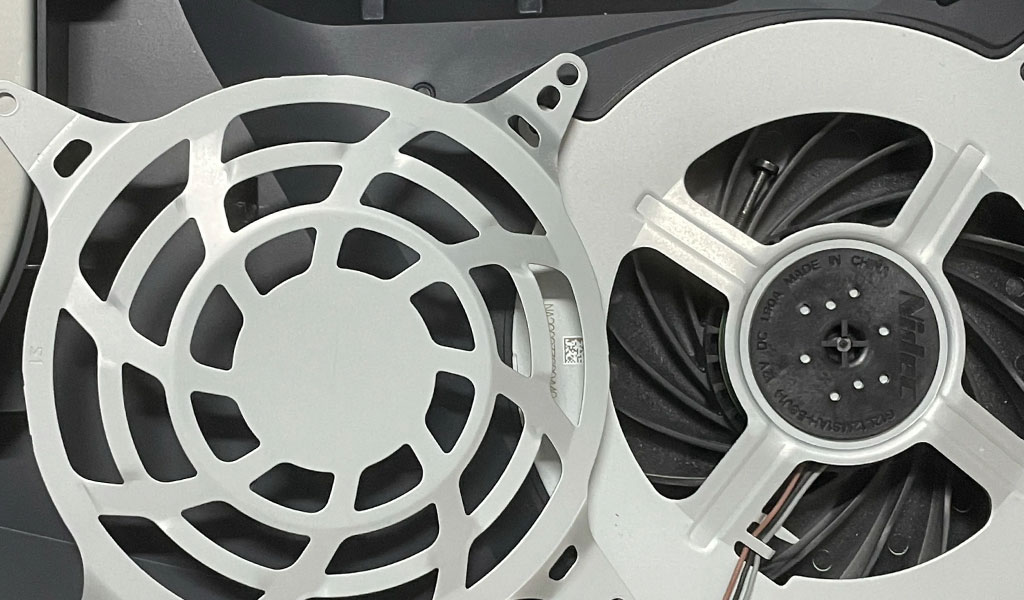
In this paper, the Flotherm electronic equipment thermal design simulation software of Flomerics is used to study the influence of the distance between the fan outlet and the radiator on the heat dissipation of the module. Temperature rise, reasonable control of thermal design redundancy, to determine the best distance between the fan outlet and the radiator, to provide a feasible solution for the structural design of power products.
Foreword
With the continuous advancement of power technology, the power density of power products has been continuously improved, and the volume of power products has also been greatly reduced. The continuous reduction of product volume requires the product structure to be compact, and the thermal design restricts the structural design. On the premise of meeting the thermal design requirements, through a reasonable and correct space layout, the space of the power supply product can be compressed to the maximum extent to improve the module’s performance. Power density happens to be the main task of thermal design optimization.
In the case of forced air cooling, due to the existence of the fan swirl, the distance between the radiator and the fan has a great influence on the uniformity of the flow field. In theory, when the distance between the radiator and the fan is large enough, the fan swirl The influence on the flow field is small. However, in the product design, due to the limitation of volume, it is impossible to allow the distance between the radiator and the fan to be too large. In other words, the influence of the fan swirl on heat dissipation must exist. This paper uses FLOTHERM thermal simulation analysis software, through reasonable control of thermal design redundancy, strives to obtain a more reasonable distance between the fan and the radiator, which provides reference for the structural design of power products.
Simulation Analysis Model
The figure below shows the simulation analysis model for the study of the effect of the distance between the fan outlet and the radiator on the heat dissipation of the module during air cooling.
In this model, the cooling air inlet temperature, that is, the ambient temperature in which the module works, is 40C. The system uses three axial fans with an external diameter of 150.0mm and a HUB diameter of 75.0mm as the cooling fans of the module. When changing the distance between the fan and the radiator, only the size of the solution domain is extended, and the radiator in the model is not changed. The size of the structure, the size of the power components, the layout position and the grid division of the radiator part, trying to make the dimensional difference between different models the distance between the fan and the radiator. At the same time, in order to well reflect the influence of the distance between the fan and the heat sink on the heat dissipation performance of the module, four temperature monitoring points are defined at the front of the module, and these monitoring points are used to display the temperature at the midpoint of the contact surface between the power device and the heat sink. The pros and cons of the cooling performance of the module can be expressed not only by the relevant information of the cooling fan operating point (mass or volume flow of the fluid, system resistance or fan operating pressure), but also by the temperature change value of the monitoring point and the solution domain space. The uniformity of the flow field is directly reflected.
Fan Operating Point And Temperature Monitoring Point
It can be seen from Figure 2 that in this module, the volume flow of the fluid flowing through the cooling fan increases with the increase of the distance between the fan and the radiator, and the increase of the volume flow is 25.0mm~75.0mm at the Distance The distance between them is particularly significant, that is to say: the flow rate of the cooling fan is very sensitive to this distance at this time, and if the distance is slightly increased, the volume flow rate of the fluid flowing through the fan will change significantly.
At the same time, when the value of Distance is between 75.0mm and 175.0mm, although the volume flow of the fan also increases with the increase of the distance in general, the increase rate is significantly lower than that of the previous stage. , that is: at this point the fan flow is in a less sensitive area for that distance. The above conclusion can also be drawn from the relationship between the pressure value and distance of the cooling fan operating point (Figure 2) and the relationship curve of each temperature monitoring point with distance (Figure 3, 4, 5, 6, etc.) Further proof can be obtained.
In Figures 3, 4, 5, and 6, it should be noted that the temperature monitoring points 1 and 2 reflect the above analysis, that is, as the distance increases, the air volume flowing through the cooling fan is strengthened, and the The heat exchange is strengthened, and the shell temperature of the power components on it is lowered to a certain extent. However, carefully observing monitoring points 3 and 4 (see Figures 5 and 6), it seems that we cannot get a reasonable explanation based on the above analysis.
Does the curve of monitoring points 3 and 4 (Figures 5 and 6) versus distance just illustrate a flaw in the above analysis? the answer is negative. In fact, the temperature monitoring points 3 and 4 have such a transformation relationship, which, to a certain extent, reflects the changing relationship between the uniformity of the flow field and the distance between the fan and the radiator in the radiator space. Further analysis, we can get a reasonable explanation by observing and analyzing the velocity distribution of the cross-section in the fan.
Uniformity Of The Flow Field In The Module
As shown in Figures 7, 8, 9, 10, 11, 12, and 13, they are respectively the mid-section velocity distribution diagrams of the fan under the premise of different distances. In the modeling process, considering that this is fan blowing cooling, the fan swirl has a greater impact on the flow field, so the fan’s swirl parameter setting is turned on in the model.
It can be seen from the following velocity distribution diagrams: under the condition of blowing, the fan swirl has a very significant influence on the flow field, and the uniformity of the flow field varies significantly with the distance between the fan and the radiator. In comparison, when the distance between the fan and the radiator is 25.0~75.0mm, the correlation between the uniformity of the flow field and the distance is larger than that when the distance is 75.0~175.0mm. With the further increase of the distance, the flow fields between the radiator teeth and the radiator inlet become more uniform, and the efficiency of the radiator is further improved. When the distance reaches or exceeds an outer diameter of the cooling fan, it can be seen from Fig. 12 and Fig. 13 that the distribution of the flow field can be considered to have reached an almost ideal state in the whole area.
In Conclusion
In practical applications, the distance between the cooling fan and the radiator cannot be arbitrarily satisfied due to the limitation of the structural arrangement and external dimensions of the product itself. So, how to reasonably and economically determine the distance between the fan and the radiator, and how to balance the contradictions among many factors? We must analyze the reasons for the difference in results and find a compromise method to determine the size of the distance reasonably and economically.
Carefully analyze the reasons for the uneven flow field. The key factors are: on the one hand, due to the existence of the HUB in the actual fan, the cooling air is blown out from the annular section of the fan, thereby forming an uneven flow field in the downstream area of the fan HUB. distribution; on the other hand, the working principle of an axial fan forces the fluid flowing through the outlet section of the fan to flow downstream in a rotating state. In fact, under the condition that the fluid flows out of the fan at a certain distance, this rotation effect can promote the mixing between the fluids, thereby forming a relatively uniform flow field distribution, as shown in Figure 12 and Figure 13. Combined with Figure 7~Figure 13, the cross-sectional velocity distribution of the fan and the curve of the temperature monitoring point with distance (Figure 3~Figure 6), we can see that when the distance between the fan and the radiator is the HUB diameter of a fan, due to the HUB The uneven flow field caused by the existence of the heat sink can be greatly improved. Although the flow field distribution is still uneven to a certain extent, the shell temperature of the power components on the radiator does not change significantly, so This asymptotic change trend curve is formed. From this we can draw the following conclusions:
- When the fan is forced to blow air for cooling, the main factor causing the uneven flow field at the downstream of the cooling fan outlet is the existence of the fan HUB, and the second is the rotation effect of the fluid flowing through the axial flow fan.
- In the structural design, in order to obtain the maximum heat dissipation capacity of the radiator, we must ensure that the distance between the cooling fan outlet section and the radiator is at least greater than the diameter of a fan HUB. However, once the distance exceeds the outer diameter of a fan, the contribution to the uniformity of the downstream flow field is very small, and the factor affecting the heat dissipation capacity of the radiator can be ignored.
- If the distance between the cooling fan outlet section and the radiator cannot be guaranteed to be at least greater than the diameter of a fan HUB in terms of structural design, a rectifier grille must be installed between the fan and the radiator.