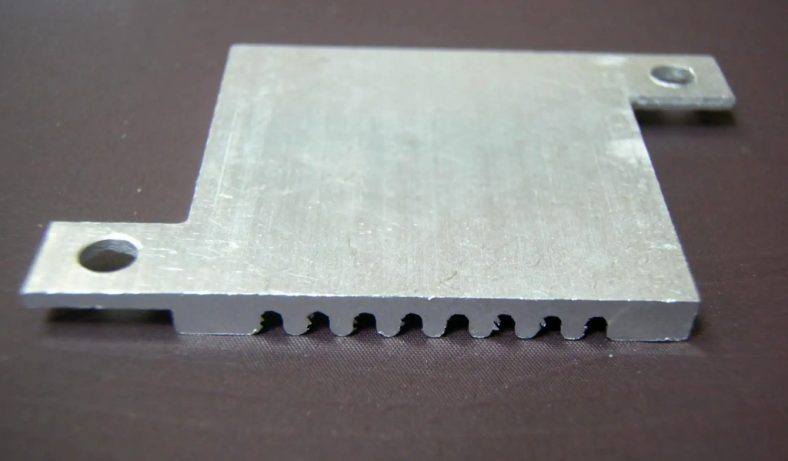
The Define Of Chip Heatsink – What Is Chip Coolers?
The chip heat sink transfers the heat generated by machinery or other appliances in the working process in time to avoid affecting the device or instrument of its normal operation. Common heatsinks can be divided into air cooling, heat pipe heatsinks, liquid cooling, semiconductor refrigeration, compressor refrigeration and other types according to the heat dissipation method.
Integrated circuits are used extensively in computer components. As we all know, high temperature is the enemy of integrated circuits. High temperature will not only cause the system to run erratically, shorten the service life, and may even cause some components to burn out. The heat that causes the high temperature does not come from outside the computer, but from inside the computer, or inside the integrated circuit. The function of the heatsink is to absorb the heat, and then dissipate it to the inside or outside of the case to ensure that the temperature of the computer components is normal. Most heatsinks absorb heat by contacting the surface of the heat-generating components, and then transfer the heat to a distance through various methods, such as the air in the chassis, and then the chassis transmits the hot air to the outside of the chassis to complete the cooling of the computer.
There are many types of heatsinks. CPUs, graphics cards, motherboard chipsets, hard drives, chassis, power supplies, and even optical drives and memory all require heatsinks. These different heatsinks cannot be mixed, and the most commonly used one is the CPU heatsink. . According to the way of removing heat from the heatsink, the heatsink of the computer can be divided into active cooling and passive cooling. The former is common with air-cooled heatsinks, while the latter is common with heat sinks. The heat dissipation method is further subdivided, which can be divided into air cooling, heat pipe, liquid cooling, semiconductor cooling, compressor cooling, etc.
The Material Of Heat Sink
Heat sink material refers to the specific material used for the heat sink. The thermal conductivity of each material is different, arranged from high to low thermal conductivity, respectively, silver, copper, aluminum, steel. However, if silver is used as the heat sink, it will be too expensive, so the best solution is to use copper. Although aluminum is much cheaper, it is obviously not as thermally conductive as copper (roughly just over fifty percent of copper).
Commonly used heat sink materials are copper and aluminum alloys, each of which has its own advantages and disadvantages. Copper has good thermal conductivity, but it is expensive, difficult to process, heavy (many pure copper heat sinks exceed the weight limit of CPU), small heat capacity, and easy to oxidize.
Pure aluminum is too soft to be used directly. Only aluminum alloys are used to provide sufficient hardness. The advantages of aluminum alloys are low price and light weight, but the thermal conductivity is much worse than that of copper. Some radiators take their own advantages and embed a copper plate on the aluminum alloy radiator base. For ordinary users, the use of aluminum heat sinks is enough to meet the heat dissipation needs.
The Cooling Method Of Heat Sink
The heat dissipation method refers to the main way that the heat sink dissipates heat. In thermodynamics, heat dissipation is heat transfer, and there are three main ways of heat transfer: heat conduction, heat convection and heat radiation. The transfer of energy in matter itself or when matter comes into contact with matter is called heat conduction, which is the most common form of heat transfer. For example, the direct contact between the CPU heat sink base and the CPU to take away heat is thermal conduction. Thermal convection refers to the heat transfer method in which the flowing fluid (gas or liquid) takes the heat away. In the cooling system of the computer case, the “forced thermal convection” cooling method in which the cooling fan drives the gas flow is more common. Thermal radiation refers to the transfer of heat by means of ray radiation, the most common of which is solar radiation in daily life. These three heat dissipation methods are not isolated. In daily heat transfer, these three heat dissipation methods all occur at the same time and work together.
In fact, any type of heat sink will basically use the above three heat transfer methods at the same time, but the emphasis is different. For example, in an ordinary CPU heat sink, the CPU heat sink is in direct contact with the surface of the CPU, and the heat on the CPU surface is transferred to the CPU heat sink through thermal conduction; the cooling fan generates airflow to take away the heat on the surface of the CPU heat sink through thermal convection; The flow also takes away the heat of the air around the CPU heat sink through thermal convection until the outside of the chassis; at the same time, all parts with high temperature will radiate heat to parts with low surrounding temperature.
The heat dissipation efficiency of the heatsink is related to the thermal conductivity of the heatsink material, the heat capacity of the heatsink material and the heat dissipation medium, and the effective heat dissipation area of the heatsink.
According to the way of removing heat from the heatsink, the heatsink can be divided into active cooling and passive cooling. To further subdivide the cooling methods, it can be divided into air cooling, heat pipe, liquid cooling, semiconductor cooling and compressor cooling, etc.
Air cooling is the most common, and very simple, is to use a fan to remove the heat absorbed by the heatsink. It has the advantages of relatively low price and simple installation, but it is highly dependent on the environment. For example, its heat dissipation performance will be greatly affected when the temperature rises and overclocking.
A heat pipe is a heat transfer element with extremely high thermal conductivity. It transfers heat through the evaporation and condensation of liquid in a fully enclosed vacuum tube. It uses fluid principles such as capillary action to achieve a cooling effect similar to that of a refrigerator compressor. It has a series of advantages such as extremely high thermal conductivity, good isothermal, heat transfer area on both sides of cold and hot can be changed arbitrarily, long-distance heat transfer, temperature control and a series of advantages, and the heat exchanger composed of heat pipes has heat transfer efficiency It has the advantages of high height, compact structure and small fluid resistance loss. Due to its special heat transfer characteristics, the tube wall temperature can be controlled to avoid dew point corrosion.
Liquid cooling is the use of liquid to force the circulation of the heatsink to take away the heat of the heatsink driven by the pump. Compared with air cooling, it has the advantages of quietness, stable cooling and less dependence on the environment. However, the price of heat pipes and liquid cooling is relatively high, and the installation is relatively troublesome.
When purchasing a heatsink, you can choose it according to your actual needs and economic conditions. The principle is that it is enough.
The Ambient Heat Exchange Of Heat Sink
After the heat is transferred to the top of the radiator, it is necessary to dissipate the transmitted heat to the surrounding environment as soon as possible. For the air-cooled radiator, it is to exchange heat with the surrounding air. At this time, heat is transferred between two different media, and the formula followed is Q=α X A X ΔT, where ΔT is the temperature difference between the two media, that is, the temperature difference between the radiator and the surrounding air; and α is the temperature difference of the fluid. Thermal conductivity, after the heat sink material and air composition are determined, it is a fixed value; the most important A is the contact area between the heat sink and the air. Under the premise that other conditions remain unchanged, such as the volume of the heat sink, there will generally be However, by changing the shape of the radiator, increasing the contact area with the air and increasing the heat exchange area, it is an effective means to improve the heat dissipation efficiency. To achieve this, the surface area is generally increased by means of a finned design supplemented by surface roughening or threads.
Pure Aluminum Heatsink
Pure aluminum heatsink is the most common heatsink in the early days. Its manufacturing process is simple and the cost is low. Pure aluminum heatsink still occupies a considerable part of the market. In order to increase the heat dissipation area of its fins, the most commonly used processing method for pure aluminum heatsinks is aluminum extrusion technology, and the main indicators for evaluating a pure aluminum heatsink are the thickness of the heatsink base and the Pin-Fin ratio. Pin refers to the height of the fins of the heat sink, and Fin refers to the distance between two adjacent fins. The Pin-Fin ratio is the height of the Pin (excluding the thickness of the base) divided by the Fin. The larger the Pin-Fin ratio, the larger the effective heat dissipation area of the heatsink, and the more advanced the aluminum extrusion technology.
Ceramic Heatsink (Also Known As Ceramic Heat Exchanger)
Its production process is basically the same as that of kiln furniture, and thermal conductivity and anti-oxidation properties are the main application properties of the material. Its principle is to place the ceramic heatsink in a place close to the flue outlet and with a high temperature, without cold air and high temperature protection. When the furnace temperature is 1250-1450 ℃, the temperature of the flue outlet should be 1000 -1300 ℃, the waste heat recovered by the ceramic heat exchanger can reach 450-750 ℃, and the recovered hot air is sent to the kiln to form a mixture with gas for combustion, which can reduce production costs and increase economic benefits. Ceramic heat exchangers have been well developed under the limitations of metal heat exchangers, because they better solve the problems of corrosion resistance and high temperature resistance, and become the best heat exchanger for recycling high temperature waste heat. After years of production practice, the results show that the ceramic heat exchanger works very well. Its main advantages are: good thermal conductivity, high high temperature strength, good oxidation resistance and thermal shock resistance, long life, small maintenance, reliable and stable performance, and easy operation. It is the best device to recover the waste heat of high temperature flue gas.
Pure Copper Heatsink
The thermal conductivity of copper is 1.69 times that of aluminum, so all other things being equal, a pure copper heat sink will be able to remove heat from the heat source faster. However, the texture of copper is a problem. Many advertised “pure copper heatsinks” are not really 100% copper. In the list of copper, copper with a copper content of more than 99% is called acid-free copper, and the next grade of copper is Dan copper with a copper content of less than 85%. Most of the pure copper heat sinks on the market for 2013 have a copper content between the two. The copper content of some inferior pure copper heatsinks is not even 85%. Although the cost is very low, its thermal conductivity is greatly reduced, which affects the heat dissipation. In addition, copper also has obvious shortcomings, high cost, difficult processing, and too large heat sink quality hinder the application of all-copper heat sinks; the hardness of red copper is not as good as that of aluminum alloy AL6063, and the performance of some machining (such as grooves, etc.) is not as good as aluminum. ; The melting point of copper is much higher than that of aluminum, which is not conducive to extrusion and other problems.
Copper-Aluminum Bonding Technology
After considering the respective shortcomings of copper and aluminum, some high-end heat sinks in the market often use copper and aluminum combined manufacturing processes. These heat sinks usually use copper metal bases, while heat sink fins are made of aluminum alloy. Of course, in addition to the copper bottom, there are also methods such as the use of copper pillars for the heat sink, which is also the same principle. With high thermal conductivity, the copper bottom surface can quickly absorb the heat released by the CPU; the aluminum fins can be made into the most favorable shape for heat dissipation by means of complex processes, and provide a large heat storage space and release it quickly. A balance has been found in all aspects.
Heat is dissipated from the CPU core to the surface of the heat sink, which is a heat conduction process. For the base of the heat sink, since it is in direct contact with a small area of high heat source, it is required that the base can quickly conduct heat away. The use of materials with higher thermal conductivity for the heat sink is very helpful to improve the thermal conductivity. It can be seen from the comparison table of heat conduction system that, for example, the thermal conductivity of aluminum is 237W/mK, and the thermal conductivity of copper is 401W/mK. Comparing heatsinks of the same volume, the weight of copper is 3 times that of aluminum, while the specific heat of aluminum is 3 times. It is only 2.3 times that of copper, so under the same volume, a copper heatsink can hold more heat than an aluminum heatsink and heat up more slowly. With the same thickness of the heat sink base, copper can not only quickly remove the temperature of heat sources such as CPU Die, but also its own temperature rise is slower than that of aluminum heat sinks. Therefore, copper is more suitable for making the bottom surface of the heat sink.
However, the combination of these two metals is relatively difficult, and the affinity between copper and aluminum is poor. thermal resistance). In actual design and manufacturing, manufacturers always try to reduce the interface thermal resistance as much as possible and avoid weaknesses, which often reflects the manufacturer’s design capabilities and manufacturing processes.