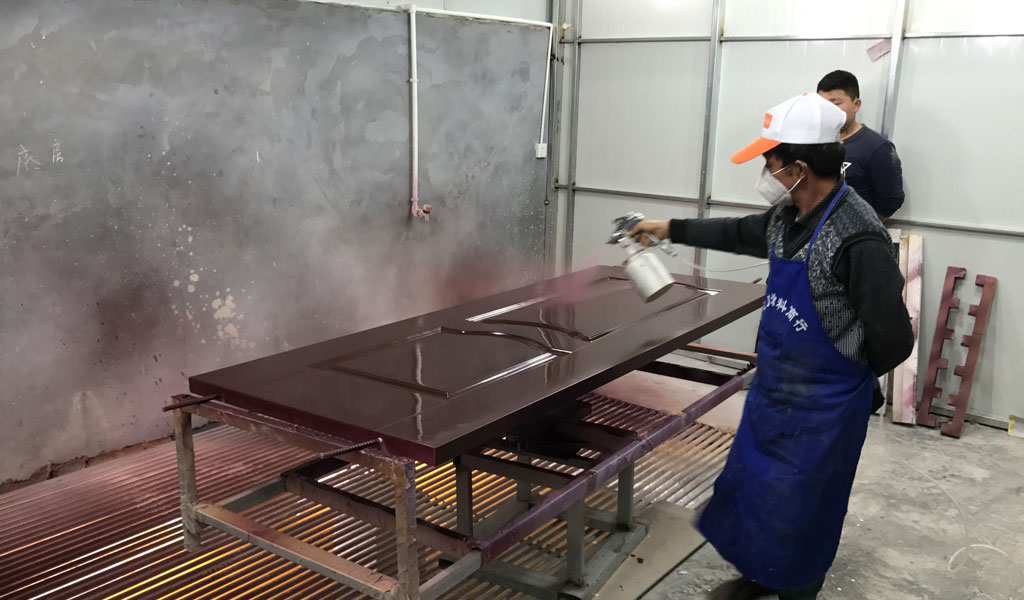
The radiator must be subjected to a water pressure test or an air tightness test before pre-treatment, and the pre-painting treatment can be carried out after strict inspection under a certain pressure for no leakage; the painted radiator is subjected to a pressure test again. As the saying goes: paint is divided into three parts and seven parts of labor. Under the premise of choosing the right paint, it is difficult to achieve the expected coating effect without a good construction. So, I have shared with you how the cathode electrophoresis tank is insulated and anti-corrosion. Now, the electrophoretic paint manufacturer Feiyang Commissioner will introduce the construction process of the anti-corrosion paint on the inner wall of the water-based radiator.
1.Pre-Processing
There are many corrosion factors in the working conditions of the heating radiator. The coating has been subjected to high temperature, high humidity and water erosion for a long time. In addition to the excellent corrosion resistance of the coating, it must also be firmly combined with the substrate. Good substrate pre-treatment; pre-treatment quality has a particularly significant impact on coating performance. It is impossible to obtain an ideal internal anti-corrosion coating without paying attention to pre-coating pre-treatment.
- The inner cavity of the radiator is small and cannot be treated by mechanical sandblasting. At present, most of them use chemical pretreatment.
- Pre-treatment process of steel radiator: finger removal→water washing→pickling→water washing→surface conditioning→phosphating treatment→water washing→drying.
- The pre-treatment process of aluminum radiator: degreasing→water washing→alkali etching→water washing→light extraction→water washing→oxidative phosphating→water washing→drying.
- Available soaking method or pump circulation method.
Tests have shown that: steel radiators with thin film phosphating will have better adhesion and impact strength, and corrosion resistance will also be improved; aluminum radiators should also control the thickness of the oxide phosphating film, and the film should not be too thick.
2.Painting
The steel and aluminum radiators are mainly poured and coated, which can be artificially or mechanically poured. That is, the radiators with qualified inner surface treatment are hoisted into a certain inclination and placement direction, and connected with the pump and the paint tank to form a circulation system. Special joint for pouring. The advantage of mechanical pouring is that it can fill multiple pieces at a time, and the efficiency is high; because the pump is transported inward, the paint liquid has a certain pressure, which can reduce the bubbles caused by shaking in the paint and avoid some shortcomings of the paint film; mechanical pouring and coating Although the efficiency has improved, there will be some delays in going up and down the joint.
When pouring, the paint liquid should be in contact with the inner wall of the radiator for more than 3 minutes and keep shaking, so that the paint liquid can fully wet the pipe wall and penetrate into the gap, so as to ensure that the paint on the inner wall of the radiator is uniform and there is no leakage.
The paint liquid in the paint can should be filtered after a period of use, and the filter cloth should be over 120 mesh to remove the residues brought in during the painting process.
3.Place Empty Paint
The radiator that has just been filled with paint cannot be baked immediately, otherwise there will be blisters in the accumulated places, the paint film on the bubbling part is incomplete, the lower part of the blisters is very thin or there is no film at all, and it is easy to be washed away by steam and water. It does not have the proper internal anti-corrosion effect.
The radiator that has just been filled with paint should be placed obliquely for 1 to 2 hours, so that the residual paint in the inner cavity will flow out. It can be placed on a shelf, or it can be hung to make it inclined as much as possible. The inclination angle should be greater than 45 degrees; it should be marked when it is vacant. The placement position of the good radiator, the first time is facing the lower end, and when the second time is filled with paint, it will be facing.
After the placement is completed, the paint accumulated in the dead corner should be sucked off with a vacuum pump to minimize the accumulation and avoid baking and foaming. For the radiator with complex shape, many dead corners in the inner cavity, and difficult for residual paint to flow out, we should find a way to make it easy to flow out the accumulated paint.
The viscosity of the paint varies greatly with temperature. When the temperature rises above 35 degrees, the viscosity of the paint decreases rapidly, which is conducive to the leveling of the paint; where conditions permit, it can be considered to heat the paint appropriately, which can improve the performance of the paint. The penetration force of the paint makes the paint leveling better and the paint hanging more uniform.
4.Baking And Curing
After painting, the radiator should be baked and cured. The first curing temperature is 140 degrees for half an hour, and the second curing temperature is 180 degrees for half an hour. When baking, it is best to lay the radiator flat and let the corners accumulate. This can reduce the accumulation and foaming of the paint; according to different situations, the curing temperature and time can be adjusted appropriately, but the premise is that the coating is completely cured.
5.Inspection And Quality Control
The inspection of each link of the coating process is very important. The inspection items mainly include:
- After the inner wall coating of the radiator is cured, it should be tested with a coating thickness gauge. After the inner coating is completed, the total thickness should be measured; because the inner cavity of the radiator is narrow, it cannot be directly measured with a thickness gauge. A batch can be dissected for testing; or a test panel made of the same material as the workpiece, pre-treated and painted together with the workpiece to measure the thickness. Magnetic thickness gauges are used for steel radiators, while eddy current thickness gauges are used for aluminum radiators.
- The appearance of the coating film should be bright and smooth, without sagging, accumulation, pores, bubbling, and no leakage.
- Conditional units should purchase an electric spark detector to thoroughly inspect the inner cavity of the radiator to ensure the quality of the anti-corrosion coating in the radiator.