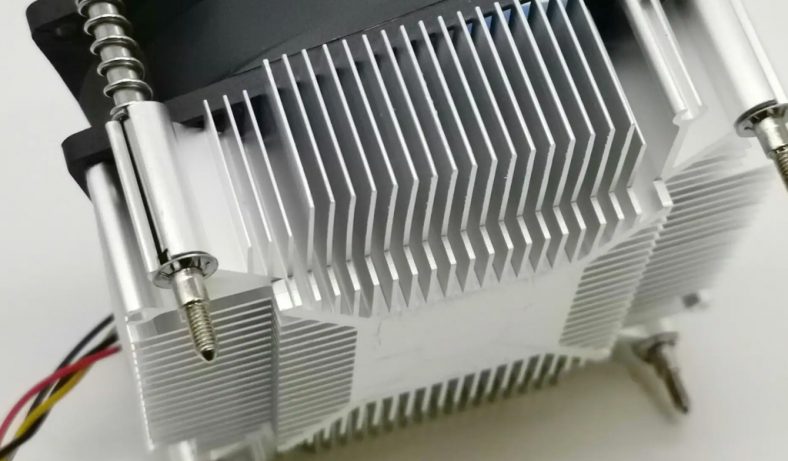
The Define Of Aluminum CPU Heat Sink
Pure aluminum heatsink is the most common heatsink in the early days. Its manufacturing process is simple and the cost is low. Pure aluminum heatsink still occupies a considerable part of the market. In order to increase the heat dissipation area of its fins, the most commonly used processing method for pure aluminum heatsinks is aluminum extrusion technology, and the main indicators for evaluating a pure aluminum heatsink are the thickness of the heatsink base and the Pin-Fin ratio. Pin refers to the height of the fins of the heat sink, and Fin refers to the distance between two adjacent fins. The Pin-Fin ratio is the height of the Pin (excluding the thickness of the base) divided by the Fin. The larger the Pin-Fin ratio, the larger the effective heat dissipation area of the heatsink, and the more advanced the aluminum extrusion technology.
Processing And Forming Technology Of Heatsink
From some perspectives, the processing and molding technology of the heatsink determines the final performance of the heatsink, and is also the most important manifestation of the manufacturer’s technical strength. The mainstream molding technologies of heatsinks are mostly as follows:
Aluminum Extrusion Technology (Extruded)
The aluminum extrusion technology is simply to heat the aluminum ingot to a high temperature of about 520~540 °C, let the aluminum liquid flow through the extrusion die with grooves under high pressure, and make the preliminary heat sink embryo, and then the heat sink preliminary embryo is processed. After cutting, grooving and other processing, the heat sinks we commonly see are made. Aluminum extrusion technology is easy to implement and the equipment cost is relatively low, which has also made it widely used in the low-end market in the past few years. The commonly used aluminum extrusion material AA6063 has good thermal conductivity (about 160~180 W/m.K) and processability. However, due to the limitation of its own material, the ratio of the thickness and length of the heat dissipation fins cannot exceed 1:18, so it is difficult to increase the heat dissipation area in a limited space, so the heat dissipation effect of the aluminum extrusion heat sink is relatively poor, and it is difficult to be competent Today’s rising high-frequency CPUs.
Aluminum Die Casting Technology
In addition to aluminum extrusion technology, another process that is often used to manufacture heat sinks is aluminum die-casting. After melting aluminum ingots into a liquid state, they are filled into metal models and directly die-casted by a die-casting machine to make heat sinks. The fins can be made into various three-dimensional shapes by the injection method. The heat sinks can be made into complex shapes according to the needs. Fins are used to increase the heat dissipation area and are widely used because of the simple process. The commonly used die-casting aluminum alloy is ADC12. Due to its good die-casting formability, it is suitable for thin castings. However, due to its poor thermal conductivity (about 96 W/m.K), AA1070 aluminum is now used as a die-casting material in China. The thermal conductivity is as high as about 200 W/m.K, which has a good heat dissipation effect.
However, the AA1070 aluminum alloy die-casting heatsink has some inherent deficiencies that cannot be overcome by itself:
- Excessive flow lines and oxide slag on the surface during die casting will reduce the heat transfer effect.
- During cooling, the internal micro-shrinkage holes are high, and the substantial thermal conductivity is reduced (K<200 W/m.K).
- The mold is easily eroded, resulting in a short life.
- Poor formability, not suitable for thin castings.
- The material is soft and easy to deform.
With the continuous increase of CPU frequency, in order to achieve better heat dissipation effect, the volume of aluminum heatsink produced by die-casting process continues to increase, which brings many problems to the installation of the heatsink. The effective heat dissipation area is limited. In order to achieve a better heat dissipation effect, the air volume of the fan must be increased, and increasing the air volume of the fan will generate more noise.