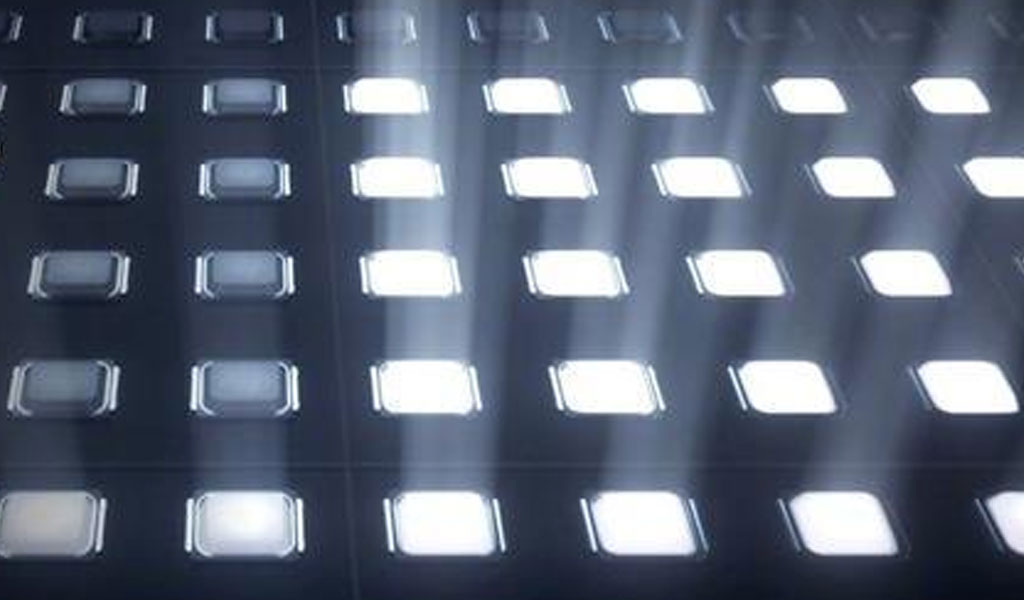
Now more and more people pay attention to the heat dissipation of LED. This is because the light decay or life of LED is directly related to its junction temperature. If the heat dissipation is not good, the junction temperature will be high and the lifespan will be short. A drop of 10°C will extend the life by 2 times. From the relationship between light decay and junction temperature released by Cree (Figure 1), it can be seen that if the junction temperature can be controlled at 65°C, the life of the light decay to 70% can be as high as 100,000 hours! This is the life that people dream of, but is it really possible? Yes, it’s possible as long as you can seriously deal with its cooling issues! Unfortunately, the heat dissipation of actual LED lamps is far from this requirement! As a result, the life of LED lamps has become a major problem affecting their performance, so it must be taken seriously!
Moreover, the junction temperature not only affects the long-term life, but also directly affects the short-term luminous efficiency
If the light emission is 100% when the junction temperature is 25 degrees, then when the junction temperature rises to 60 degrees, the light emission is only 90%; when the junction temperature is 100 degrees, it drops to 80%; at 140 degrees, it is only 70%. It can be seen that it is very important to improve heat dissipation and control the junction temperature.
In addition, the heating of the LED will also make its spectrum shift; the color temperature will increase; the forward current will increase (when constant voltage power supply); the reverse current will also increase; the thermal stress will increase; the aging of the phosphor epoxy resin will accelerate, etc. There are various problems, so the heat dissipation of LED is the most important issue in the design of LED lamps.
The First Part Of LED Chip Heat Dissipation
How Is The Junction Temperature Generated?
The reason why the LED heats up is because the added electrical energy is not all converted into light energy, but a part of it is converted into heat energy. The light efficiency of LED is currently only 100lm/W, and its electro-optical conversion efficiency is only about 20~30%. That is to say, about 70% of the electrical energy is turned into heat energy.
Specifically, the generation of LED junction temperature is caused by two factors.
- The internal quantum efficiency is not high, that is, when electrons and holes are recombined, photons cannot be generated 100%, which is usually referred to as “current leakage”, which reduces the recombination rate of carriers in the PN region. The leakage current multiplied by the voltage is the power of this part, which is converted into heat energy, but this part does not account for the main component, because the internal photon efficiency is now close to 90%.
- The photons generated inside cannot be all emitted to the outside of the chip and finally converted into heat. This part is the main part, because the current quantum efficiency called external is only about 30%, and most of it is converted into heat.
Although the luminous efficiency of the incandescent lamp is very low, only about 15lm/W, it converts almost all the electrical energy into light energy and radiates it out. Because most of the radiant energy is infrared, the luminous efficiency is very low, but it eliminates the cooling problem.
The Heat Dissipation Of The LED Chip To The Base Plate
LED chips are characterized by the generation of extremely high heat in an extremely small volume. The heat capacity of the LED itself is very small, so the heat must be conducted out at the fastest speed, otherwise a high junction temperature will be generated. In order to draw the heat out of the chip as much as possible, many improvements have been made on the chip structure of the LED.
In order to improve the heat dissipation of the LED chip itself, the main improvement is to use a substrate material with better thermal conductivity. Early LEDs just used Si silicon as a substrate. Later, it was changed to sapphire as the substrate. However, the thermal conductivity of the sapphire substrate is not very good (about 25W/(m-K) at 100°C). In order to improve the heat dissipation of the substrate, Cree uses a silicon carbide substrate, and its thermal conductivity (490W/( m- K)) is nearly 20 times higher than that of sapphire. Moreover, sapphire needs to be solidified with silver glue, and the thermal conductivity of silver glue is also very poor. The only disadvantage of silicon carbide is that it is more expensive. Currently only Cree produces LEDs based on silicon carbide.
After using silicon carbide as the substrate, it can indeed greatly improve its heat dissipation, but its cost is too high, and it has patent protection. Recently, domestic manufacturers have begun to use silicon materials as substrates. Because the substrate of the silicon material is not limited by the patent. And the performance is better than sapphire. The only problem is that the expansion coefficient of GaN is too different from that of silicon, which makes it prone to cracking. The solution is to add a layer of aluminum nitride (AlN) in the middle as a buffer.
After the LED chip is packaged, the thermal resistance from the chip to the pin is the most important thermal resistance in the application. Generally speaking, the size of the junction area of the chip is the key to heat dissipation. For different rated power, the corresponding size is required. junction area. It is also manifested as different thermal resistances.
The early LED chips mainly rely on two metal electrodes to lead to the outside of the chip. The most typical one is the straw hat tube called ф5 or F5. Its heat dissipation is completely led out by two thin metal wires, so the heat dissipation effect is very poor. The thermal resistance is very large, which is why the light decay of this straw hat tube is very serious. In addition, the material used in packaging is also an important issue. Low-power LEDs usually use epoxy resin as the encapsulation material, but the absorption rate of epoxy resin to 400-459nm light is as high as 45%. The life of light decay is less than 10,000 hours. Therefore, silica gel must be used as the packaging material in high-power LEDs. Silica gel absorbs less than 1% of light of the same wavelength. Thus, the life of the same light decay can be extended to 40,000 hours.
The thermal resistance of Cree’s LED is at least twice lower than that of other companies because of the use of silicon carbide as the substrate. In order to improve heat dissipation of high-power LEDs, a solderable copper base plate is usually placed under the substrate for soldering to the heat sink. These thermal resistances are actually measured on this copper base.
Is silicon carbide the best choice for LED substrates? No, everything will be innovated and developed. Recently, Taiwan’s Diamond Technology has developed Diamond Islands Wafer (DIW) as a super LED. substrate. The thermal resistance of this LED can be as low as <5°C/W. Super LEDs made with it emit extremely strong ultraviolet light, which is not reduced by high temperature, but brighter.
Moreover, using ultraviolet rays to excite various phosphors can also obtain LEDs of various colors required. Moreover, the phosphor is not mixed with epoxy resin or silica gel, but is directly coated on the surface of the chip to avoid light decay due to the aging of epoxy resin and silica gel.
This will revolutionize the entire LED. And got rid of the patent shackles of Japan and the United States and other countries.
Heat Dissipation Of Integrated LED
Many manufacturers now integrate many LED dies together to obtain high-power LEDs. The power of such LEDs can reach more than 5W, and most of them appear in power levels of 10W, 25W, and 50W. In order to connect multiple LED dies (in Eutectic or Flip-Chip packages) together, because these dies are extremely fine, precise printed circuit connections are required. In order to obtain better heat dissipation characteristics, a ceramic substrate is usually used. This ceramic substrate is composed of aluminum oxide and aluminum nitride.
Regardless of aluminum nitride or aluminum oxide, they are an insulating ceramic material, so printed circuits can be made on them. But aluminum nitride has 10 times higher thermal conductivity, so it is more commonly used now. Thick-film circuits have been used in the past, but they have uneven surfaces, rough circuit edges, and require sintering temperatures above 800°C. Now most of the thin-film circuits are used, because it only needs a process below 300 degrees, the surface flatness can be <0.3um, there will be no oxide generation, good adhesion, fine circuits, and the error is less than +/-1%
The same method is used for the production of aluminum nitride.
The Second Part Of LED Lamps Heat Dissipation
The heat dissipation of the LED chip is mentioned above, but any LED will be made into a lamp, so the heat generated by the LED chip is always dissipated into the air through the shell of the lamp. If the heat dissipation is not good, because the heat capacity of the LED chip is very small, a little heat accumulation will rapidly increase the junction temperature of the chip. If it works at a high junction temperature for a long time, its life will be shortened quickly. However, there are many ways for this heat to actually lead out of the chip to the outside air. Specifically, the heat generated by the LED chip comes out of its metal heat sink, first passes through the solder to the PCB of the aluminum substrate, and then passes through the thermal paste to the aluminum heat sink. Therefore, the heat dissipation of LED lamps actually includes two parts: heat conduction and heat dissipation. Now let’s take a look at the thermal conductivity of each link.
Thermal Conductivity Of Various Circuit Substrates
Before connecting the LEDs to the heat sink, they must be soldered to the circuit first, because first these LEDs must be connected into several strings and parallels, and at the same time, they must be connected on the circuit with the constant current source. The easiest way is to solder them directly to a normal printed board. For some very small power LEDs, such as LED indicators, this is indeed possible. However, for most high-brightness and high-power LEDs, the thermal conductivity of ordinary glass fiber printed boards is too poor, and must be changed to copper substrates or aluminum substrates or even ceramic copper clad laminates.
Aluminum Substrate
At present, aluminum substrates are used in almost the vast majority of LED lamps. The copper foil of the circuit on the aluminum substrate should have sufficient thickness and width in order to conduct electricity and heat conduction, and its thickness is between 35 μm and 280 μm. Its width is best to cover the entire substrate as much as possible in order to carry the heat down. The lower layer of insulator requires good insulation performance and good thermal conductivity. However, these two properties are contradictory. Usually, conductors have good thermal conductivity, while insulators have poor thermal conductivity. It is difficult to achieve good thermal conductivity and good insulation. It is also a research topic. At present, a modified epoxy resin or epoxy glass cloth bonding sheet mixed with ceramic fillers is used. The copper foil insulator and the aluminum plate are bonded together by hot pressing. For some LED lamps, although the radiator is carefully designed, it breaks down quickly. The problem lies in the use of aluminum substrates with high thermal resistance or aluminum substrates with poor peel strength. After a period of time, the circuit film will warp up, and it will not be able to conduct heat at all, and the LED will soon be burned out.
For high-quality aluminum substrates, its thermal resistance is usually required to be less than 1°C/W.
Foreign countries and Taiwan have been able to produce an “all-plastic aluminum substrate”. The so-called full glue means that its insulating layer does not use insulating cloth at all, but uses an insulating glue. The thermal resistance of an aluminum substrate with insulating cloth is actually typically 1.7-3.2°C/W. The thermal resistance of the all-plastic aluminum substrate can be as low as 0.05°C/W, and the products sold in the market can also be as low as 0.2-0.5°C/W.
A better performance aluminum substrate is to use the ceramic printed circuit directly on the aluminum plate. First, a 100-μm-thick aluminum oxide film is grown on the surface of aluminum by micro-arc oxidation, and then the circuit layer is fabricated by sputtering or screen printing. The biggest advantage of this method is that it has strong bonding force, and the thermal conductivity is as high as 2.1W/m.K, and the thermal expansion coefficient of the oxide layer is similar to that of aluminum, so its peel strength is as high as 5N/mm or more. It is only because the processing and manufacturing process of this ceramic aluminum substrate is complicated and the cost is high, so it is rarely used.
Although the aluminum substrate is only a special printed circuit board, it undertakes a heavy heat dissipation task. Not only the thermal conductivity of the insulating layer is better, the bonding should be firm, but also its shape must match the shape of the radiator. For example, In street lights, it is usually a rectangular shape, in spotlights, it is usually round, and in fluorescent lights, it is usually elongated. In order to obtain better thermal conductivity, copper substrates with better thermal conductivity are sometimes used, but their prices are more expensive. And in the end, it still has to be connected to the aluminum radiator. There may be a problem of cracking due to different thermal expansion coefficients.
Thermally Conductive Adhesive And Thermally Conductive Double-Sided Tape
Although the aluminum substrate has solved the problem of connecting the LED to the circuit with the aluminum plate as the substrate, the heat can be transferred to the aluminum plate, but unfortunately, the aluminum plate is often not the final heat sink, and the aluminum plate is usually connected to the real heat sink. on the radiator. The easiest way is to attach to the heatsink with rivets or screws. But this method tends to create air gaps, and very small air gaps can create thermal resistances that are dozens of times larger than others. Because the thermal conductivity of air is 0.023W/m•k. Therefore, thermal paste must be applied to fill the voids. The thermal conductivity of general thermal silica is about 1-2W/m•k.
However, the thermal conductive adhesive must have good fluidity, otherwise, there will still be air gaps due to uneven application, which may be worse than not using it. Another disadvantage of thermal paste is that it is not sticky enough to fix the aluminum substrate to the aluminum heat sink.
So another method is to use a double-sided film with strong adhesion and thermal conductivity. This thermal conductive film is a viscous thermal conductive sheet made of acrylic series materials, which is a heat dissipation material with viscosity and low thermal resistance. Moreover, it has thermal conductivity and flexibility, and can be closely attached to the uneven parts of the parts, thereby preventing the existence of air gaps. The thermal conductivity of thermally conductive silicone sheets is usually between 2-3W/m•k. Its tensile strength can reach 8kg/cm2. Enough to bond aluminum substrate and aluminum heat sink. The withstand voltage can reach 4KV/mm.
Flexible Printed Board
From the construction of the aluminum substrate, one must have the question, why the printed circuit should be glued to a thin aluminum plate first instead of directly glued to the heat sink? This can also save drilling, applying thermal conductive glue, screwing and other processes, and can also save the thermal resistance of the thermal conductive glue. The main reason is that the shape of the radiator is generally not a simple plane, and it is difficult to bond by thermocompression, and the radiator is designed and manufactured by a lighting factory, while the aluminum substrate is manufactured by a printed board factory. The solution to this problem is to use a flexible printed board and attach it to the aluminum heat sink.
The LEDs Are Soldered Directly To The Aluminum Heat Sink.
This is a more revolutionary radical solution. For high-power LEDs above 1W, usually its heat-dissipating copper base plate is insulated from the two electrodes. In order to allow it to dissipate heat more directly, it is best to solder its heatsink base plate directly to the heatsink. However, the general radiator is made of aluminum alloy and cannot be welded. Of course, this problem can be solved if a copper heat sink is used, but the price and weight are unacceptable. An easy fix is to sputter copper on the aluminum heatsink. Then punch holes in the flexible printed board, so that the copper base plate of the LED is directly exposed on the heat sink surface, and then use low-temperature solder for soldering. This method can eliminate the thermal resistance of the aluminum substrate and the thermal resistance of the thermally conductive silicone or silicon wafer. Thereby greatly improving the heat dissipation efficiency. In conclusion, the less interface between the LED and the heat sink, the better.
Heat Pipe Heat Conduction
In many occasions, the heat generated by the LED needs to be transferred to the heat sink at the fastest speed, which is especially important in the use of integrated monolithic high-power LEDs, because its heat is very large (power can reach 50W-100W) and Very concentrated (sometimes only 30mm), at this time, heat pipes must be used to dissipate heat.
Heat pipes are also known as phase change heat conductors because the liquid in them conducts heat from a liquid phase to a gas phase. Its thermal resistance is very small, about 0.065°C/W.
The inner wall is sintered with copper powder, so that the heat carrier that changes back to the liquid phase can be adsorbed on it and refluxed. However, the heat pipe can only transmit heat to the far end, and does not dissipate the heat into the air. Therefore, even if a heat pipe is used, an ordinary aluminum radiator is still required to dissipate the heat. It should be reminded again that after the copper heat pipe is used, special attention should be paid to the joint part between it and the aluminum substrate at the front and the aluminum radiator at the rear must be in close contact with each other and prevent it from being detached due to the difference in thermal expansion coefficient. The joints should be coated with high-quality thermally conductive silica gel. The better thermal conductivity is the loop heat pipe.
The biggest advantage of the loop heat pipe is that it can conduct heat in a cycle without external power devices, has a long heat conduction distance, a large transmission power (hundreds of watts), a variety of shapes and is not limited by gravity requirements, which means that it can be placed arbitrarily. After Taiwan’s Yangjie Technology Co., Ltd. adopted the loop heat pipe technology, the 150W LED street light weighs only 8.5 kilograms, and the 100W LED street light weighs only 5.5 kilograms.
Thermal Resistance Of The System
The heat generated by the LED chip comes out of its metal heat sink, first passes through the solder to the PCB of the aluminum substrate, and then passes through the thermally conductive adhesive to the aluminum heat sink. To quantitatively understand the heat dissipation process of LED chips, it is best to use the concept of thermal resistance. Heat is like electric charge, and heat flows like electric current. In the process of flowing, it will encounter resistance, just like resistance, here we call it thermal resistance. Thermal resistance is measured in degrees per watt (°C/W), which is how many degrees rises for every 1 watt of power flowing through it. If you know the power required to dissipate, and you know its thermal resistance, you can know what its temperature rise is. The larger the thermal resistance, the less heat can flow, and the higher the temperature rise; the smaller the thermal resistance, the faster the heat flow, and the smaller the temperature rise. The figure shows that heat flows from the LED chip to the air through many different thermal resistances:
- Rj1: The thermal resistance from the chip to the mounting base plate (that is, the thermal resistance of the chip)
- Rj2: Thermal resistance of solder
- Rj3: Thermal resistance of aluminum substrate
- Rj4: Thermal resistance of thermally conductive silicone
- Rj5: Thermal resistance from heat sink to air
So the total thermal resistance from chip to air should be:
Rja=Rj1+Rj2+Rj3+Rj4+Rj5
As long as you know the total thermal resistance from the chip to the air, you can calculate the junction temperature according to the power Pd that needs to be dissipated. Knowing the junction temperature can also know its life.
Assuming the ambient temperature is Ta, then the junction temperature is:
Tj = Pd(Rj1+Rj2+Rj3+Rj4+Rj5)+Ta
However, in actual LED lamps, the thermal resistance from the LED chip to the air is much more than this. For example, the thin-film printed board is usually mounted on an aluminum substrate, and the aluminum substrate is mounted on the aluminum heat sink. Apply thermal paste, the thickness of thermal paste is difficult to estimate, and there are still residual air gaps. For lamps with heat pipes, the gap between the heat pipe and the heat dissipation fins and the thermal resistance of the thermal conductive adhesive should also be considered.
And the most difficult to estimate is Rj5, which is the thermal resistance of the heat sink to air. This involves a lot of heat dissipation mechanisms related to convection and radiation.
It should be noted that when calculating the heat dissipation of the LED, a common mistake is to take the full power of the LED as its dissipated power Pd. For example, a 1W LED has a forward voltage of 3.3V and a forward current of 350mA. So take the product of these two 1.155 watts as its dissipation power. This is wrong. Because this is only its input power, not its dissipated power. A portion of the input power becomes useful light and is emitted. The part that needs to be dissipated as heat should be the input power minus the part that is emitted in the form of useful light, which is the part that needs to be dissipated as heat. But this part is more difficult to calculate. In general, because the luminous efficiency of LEDs varies, this dissipated power varies. Generally speaking, the following approximation can be made: the luminous efficiency is 100lm/W, and the dissipated power should be 70% of the input power. For the 1W LED mentioned above, that is, 1.155×0.7=0.8W becomes useless. Heat needs to be dissipated.
So if we know the thermal resistance of all parts, we can know the total thermal resistance of the LED lamp, and we can know the junction temperature of the LED chip, and we can know the life of the lamp?
The situation is far from simple. Although we can carefully analyze the thermal resistance of each part, and even get more accurate numbers, there are still many important factors that we have overlooked. Because the above model is just a model of a single LED luminaire, and the actual luminaire is much more complicated than this model.
- Distribution of LEDs. In many cases, LED lamps are composed of many LEDs instead of just one LED. Probably all these LEDs are soldered on an aluminum substrate. At this time, if only the thermal resistance of the standard aluminum substrate is used to calculate the thermal resistance of the entire lamp, there will be a big difference. Because the heat dissipation of each LED is affected by the heat emitted by the surrounding LEDs. In other words, the thermal resistance of the aluminum substrate is difficult to calculate at this time.
- The influence of other heat sources, such as the constant current power supply of LEDs, is an important heat source. If this heat source is close to some LEDs, the heat dissipation of these LEDs will be significantly reduced and their lifespan will be shortened. It is also equivalent to changing its thermal resistance.
- Thermal resistance actually only considers heat conduction, not convection and radiation at all. The heat starts from the LED chip, passes through a series of different materials, and finally reaches the finned heat sink. The heat will eventually be dissipated into the air. If it is not dissipated into the air, then this heat will also accumulate, causing the junction temperature to rise. Therefore, it can be said that the last part of the fin radiator dispersing into the air is the most critical part, the most complicated part, and the most difficult part to calculate. In other words, Rj5 is basically impossible to calculate with simple calculations. This makes it almost impossible to calculate the junction temperature of the LED from the thermal resistance of all components.
Radiator Design
When it comes to radiators, there is a concept that must be clarified first, that is, the difference between heat conduction and heat dissipation. Thermal conduction is to transfer heat from the heat source to the surface of the radiator as quickly as possible, while heat dissipation is to dissipate heat from the surface of the radiator to the air. First, the heat should be exported as quickly as possible, and then it should be dissipated into the air most efficiently. Because no matter what method is used to dissipate heat, the heat can only be dissipated into the air in the end. There are only two ways to dissipate heat: convection and radiation.
Convective Cooling And Radiation Cooling
For convection heat dissipation, the basic formula is as follows:
Q = h•A•△T
Where Q is the heat dissipated, h is the thermal convection coefficient, A is the heat dissipation area of the radiator, and ΔT is the temperature difference between the surface of the radiator and the nearby air.
The heat dissipation of fins mainly depends on convection and radiation, among which convection is the most important. Both parts depend on the total area of the fins. The larger the area, the better the heat dissipation effect. However, convection heat dissipation is not completely determined by the size of the fin area, but also related to the wind direction, and in a completely windless state, it is related to the resistance of natural convection. For example, if the fins are installed facing downwards to prevent dust and bird droppings from accumulating, the ends of the fins cannot be blocked, and the lamps are inclined either downwards or upwards to allow the hot air to flow smoothly.
The heat dissipation formula of thermal radiation is “Q=E×S×F×Δ(Ta-Tb)”. In the formula, Q represents the ability to exchange thermal radiation, and E is the thermal radiation coefficient of the surface of the object. In practice, when the material is metal and the surface is smooth, the thermal emissivity is relatively small, and the surface thermal emissivity value will increase after the metal surface is treated (such as blackening). Most of the thermal emissivity values of plastics or non-metals are relatively high. S is the surface area of the object, F is a function of the angle of radiative heat exchange and the surface, but this function is more difficult to explain here. Δ(Ta-Tb) is the temperature difference between the temperature of surface a and surface b. Therefore, there is a proportional relationship between the amount of thermal radiation and the thermal radiation coefficient, the size of the surface area of the object and the temperature difference. The emissivity of an absolute black body is 1. Radiation heat dissipation can also be expressed by another formula:
Heat dissipation of thermal radiation [W]=5.67×10-8x emissivity x radiator area [m2] x (average temperature + 273) 3x (temperature difference) [°C]
The thermal emissivity is not only related to the material, but also to the processing.
Oxidation treatment is an important way to improve the radiation heat dissipation of materials. A considerable part of the heat dissipation of cast iron radiators relies on radiation heat dissipation. Moreover, the thermal radiation performance of plastic is similar to that of oxidized metal.
In order to improve radiation heat dissipation, the aluminum alloy fin radiator needs to be blackened, but some people use the method of spraying black plastic paint. Although this method also makes the surface black, in fact, an insulating layer is added. , hindering its cooling. The best way is to use anodized blackening treatment. This oxide layer can be made very thin and will not affect its heat dissipation, but it has a great improvement in radiation heat dissipation.
In short, both convection and radiation are proportional to the heat dissipation area of the radiator, so to improve heat dissipation, the area of the radiator must be increased.
Fin Heat Sink
The radiator adopts the shape of fins to increase the heat dissipation area. In order to facilitate radiation heat dissipation and convection heat dissipation. The most important indicator of the radiator is its heat dissipation area A, but the heat dissipation effect of different parts of the radiator is different. The heat dissipation at the root is poor, and the heat dissipation at the top is good. So the radiator has an effective heat dissipation area. It is usually around 70% of the actual area. From experience, it generally takes about 50-60 square centimeters of effective heat sink area to dissipate 1W of power.
The material of the radiator is usually aluminum alloy. Compared with copper, although its thermal conductivity is only half of that of copper, it is light in weight, easy to process and cheap, so it is widely used in radiators.
In order to increase the heat dissipation area, the method of increasing the height is usually adopted. However, after the height increases to a certain extent, its effect will become smaller and smaller.
After the height is increased to 40mm, the decrease of junction temperature is very slow. Increasing the length is also a way to increase the area. But not the longer the better. After the length increases to a certain extent, the junction temperature will not only not decrease, but will instead increase. This is because the flow of air along the length is hindered (mainly for vertically placed fins).
Therefore, for the radiator, in addition to increasing the area, how to accelerate the convection of the air is very important, especially the street lights installed outdoors such as LED street lights are more important. Since the outdoor wind direction is uncertain, in order to have good convection in various wind directions, it is best to use a needle fin radiator. But this also reduces its equivalent heat dissipation area by a large percentage.
Zhu Nanke applied the needle-shaped heat sink to LED street lamps for the first time. It is said that this can reduce the junction temperature of the LED by more than 15 degrees and improve the life of the LED.
The heat dissipation effect of street lamp radiators is often greatly reduced due to the accumulation of dust and bird droppings, so it is usually avoided by installing downwards, but this will reduce the effect of air convection, because the hot air flows upwards . It is usually necessary to have an inclination angle during installation to improve.
Forced Air Cooling
At present, almost the vast majority of LED lamps use natural air convection to dissipate heat. However, the heat dissipation effect of convection is closely related to the air velocity. In a 15W LED lamp, if forced air cooling is used, the relationship between the junction temperature of its LED and the wind speed can be obtained.
In the CPU of the computer, the forced air cooling system with a small fan has always been used to dissipate heat. So can a fan be used in the LED to dissipate heat?
At present, the most powerful LED lamps are LED street lamps. The biggest difference between LED street lights and computers is that they are installed in very harsh outdoor conditions. If a fan is used, it must also be able to withstand very harsh environmental conditions. For example, it must be able to be waterproof, moisture-proof, dust-proof, able to withstand the test of high and low temperature, and so on. And it can’t consume a lot of power by itself.
Recently, Taiwan Sunon company launched the world’s smallest, thinnest, and lowest power consumption “mm technology fan and blower fan MightyMini Fan & Blower. And it is used for LED lamps of various powers. For example, when applied to LED bulbs, it can break through 9W. At the same time, the LED heat dissipation module designed by the new “One-module” concept is displayed, which modularizes the heat dissipation of LED lamps. One heat dissipation module can be applied to a variety of LED lamps and simplifies the design process of the client. Several power levels of 7-15W, 10-25W, and 25-40W can be launched to dissipate heat, which can be applied to the heat dissipation of various LED application products such as LED ball lights, down lights, MR16 projection lights, and LED track lights.
Conclusion
At present, the luminous efficiency of LEDs is still relatively low, which causes the junction temperature to rise and the lifespan to decrease. In order to reduce the junction temperature to increase the life, it is necessary to pay great attention to the problem of heat dissipation. The heat dissipation design of the LED must start from the chip to the entire heat sink, and every link must be given full attention. Improper design of any link will cause serious heat dissipation problems. In the past, a large number of failures of LED street lights in long-term work were caused by more than half of the lack of heat dissipation design, and the other half was caused by power failure. Therefore, the design of heat dissipation must be given full attention.
As the light efficiency of LED increases year by year, its heat generation problem will gradually decrease. I believe that one day we will see the emergence of LED lamps that do not require heat sinks!