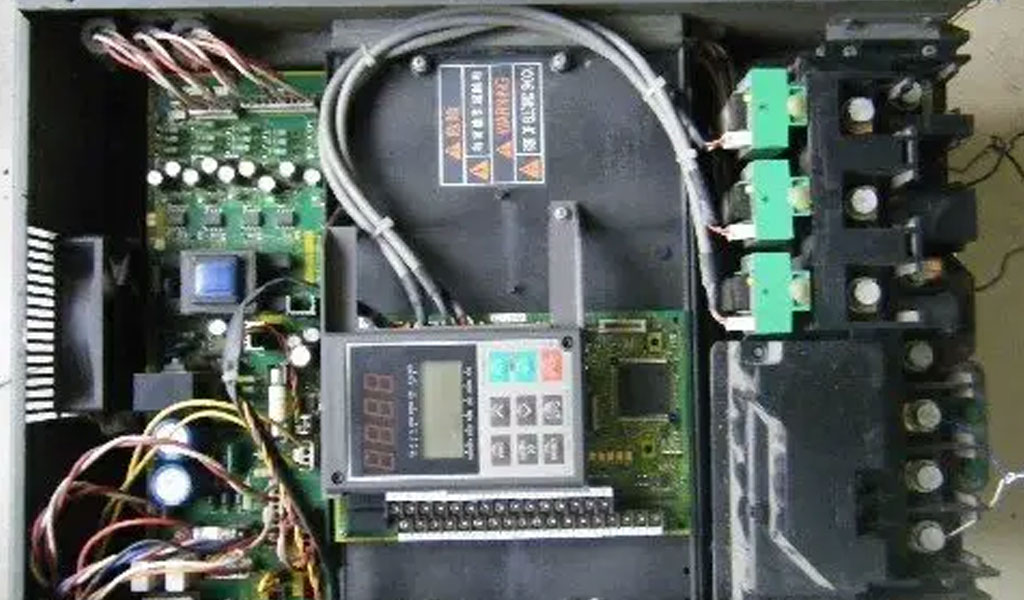
The current workaround is as follows:
- Increase the power of the components of the equipment control system (that is, expand the capacity of the components, reduce the heat generation of the heating components, and ease the heat dissipation time between the heat source and its own metal box) – Disadvantages: slow heat dissipation, large volume, and cannot be installed with a frequency converter.
- Increase the heat dissipation diameter of the metal-sealed box, and use a forced air cooling fan to force the heat-dissipation of the metal-sealed box. – Disadvantages: high production costs, difficult maintenance, and inability to install frequency converters.
- Add the water pipe coil of the metal-sealed box, so that the heat of the metal-sealed box can be taken away by the water in the process of passing through the water channel. – Disadvantages: high production cost, difficult maintenance, and frequent replacement of large amounts of cooling water.
- The heat pipe dissipates heat. The heating element in the metal sealed box is attached to one end of the heat pipe of the box, and the medium in the heat pipe is used to transfer heat to the outside of the metal sealed box. – Disadvantages: Disadvantages: large volume, high production cost, difficult maintenance, high requirements for the use of ambient temperature (must be below 25 ℃, generally used in mines).
The root cause of this main disadvantage is that the thick metal-sealed explosion-proof box is used as a medium to exchange the internal heat to the outside world, and although the latter uses forced air cooling, forced water cooling, and heat pipe media, the speed of heat exchange is still It is far from the working environment requirements of the industrial equipment control system in the explosion-proof field (slow heat dissipation, easy aging of components, short service life), and the above working principle is only heat dissipation.