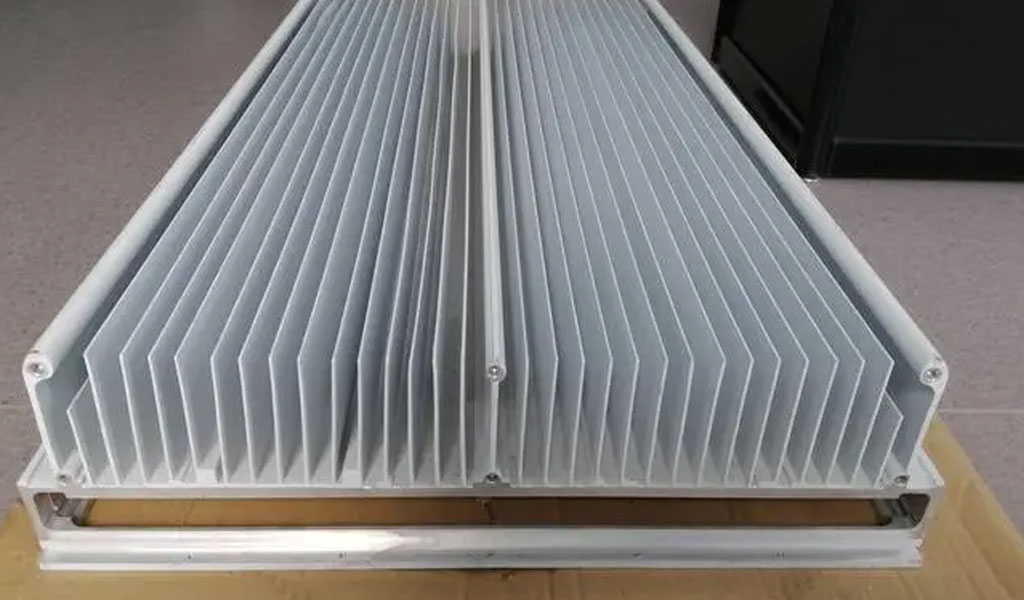
In our technologically driven world, electronic devices are becoming increasingly powerful and compact. From high-performance CPUs in computers to advanced GPUs in gaming consoles, these devices generate a significant amount of heat during operation. Excessive heat can lead to performance degradation, reduced lifespan, and even catastrophic failures. This is where heat sinks come into play. In this comprehensive article, we will delve into the intricate workings of heat sinks, exploring their design, principles of operation, and the crucial role they play in maintaining the optimal functioning of electronic components.
Understanding Heat Generation
Before we dive into the world of heat sinks, it’s important to understand the fundamental process that leads to heat generation in electronic devices. The primary source of heat in these devices is the electrical resistance encountered by the flow of electric current. According to Joule’s law, as current flows through a conductor with resistance, energy is converted into heat. This heat accumulates within the device, raising its temperature.
In devices like CPUs, GPUs, and power amplifiers, the electrical components are packed closely together, leading to a concentration of heat. If left unchecked, this heat can cause the device to exceed its safe operating temperature, resulting in performance issues and potential damage.
Enter the Heat Sink
A heat sink is a passive cooling solution designed to dissipate excess heat from electronic components. It acts as a thermal bridge between the hot component and the surrounding environment, allowing heat to flow away from the source and dissipate into the air or another medium.
Principles of Heat Transfer
To understand how heat sinks work, we need to grasp the principles of heat transfer. There are three primary modes of heat transfer:
- Conduction: This mode involves the transfer of heat through direct contact between materials. In the context of a heat sink, it refers to the transfer of heat from the hot component to the heat sink itself.
- Convection: Convection relies on the movement of fluids (liquid or gas) to carry heat away. In the case of a heat sink, this often involves using airflow to carry heat away from its fins.
- Radiation: All objects emit electromagnetic radiation as a result of their temperature. However, this mode of heat transfer is usually not as significant in the context of heat sinks for electronic devices.
Anatomy of a Heat Sink
A typical heat sink consists of several key components:
- Base Plate: The base plate of the heat sink is in direct contact with the hot electronic component. It provides a path for heat to transfer from the component to the heat sink.
- Fins: Fins are thin projections that extend from the base plate. They increase the surface area of the heat sink, allowing for enhanced heat dissipation through convection.
- Heat Pipes (Optional): Some advanced heat sinks feature heat pipes, which are hollow tubes containing a working fluid. These pipes efficiently transport heat from the base plate to the fins, where it can be dissipated.
- Mounting Mechanism: Heat sinks are typically attached to the electronic component using thermal paste or thermal pads. This ensures effective thermal contact and minimizes air gaps that could hinder heat transfer.
Modes of Heat Sink Operation
Heat sinks operate using a combination of conduction, convection, and radiation. The heat generated by the electronic component is conducted through the base plate and into the heat sink. From there, the heat spreads through the fins, which are exposed to the surrounding air.
Conduction Within the Heat Sink
The base plate of the heat sink is engineered to have high thermal conductivity, often using materials like copper or aluminum. These materials efficiently conduct heat from the hot component to the rest of the heat sink.
Convection and Airflow
Convection plays a crucial role in the heat dissipation process. As the fins of the heat sink become hot due to conduction, they heat up the surrounding air. Hot air is less dense and tends to rise, creating a natural upward airflow around the fins.
In many cases, to enhance the convective heat transfer, fans are used to force air over the fins. These fans accelerate the movement of air, allowing for a more efficient transfer of heat from the fins to the environment. This is a common setup in computers and other electronic devices where space constraints or high heat loads require active cooling solutions.
The Significance of Fin Design
The design of the fins on a heat sink significantly impacts its performance. Factors such as fin density, thickness, and spacing influence the surface area available for heat exchange. Thinner fins with closer spacing provide more surface area for heat dissipation, but they can also increase air resistance, potentially reducing overall airflow. Balancing these factors is critical in achieving optimal heat sink performance.
Types of Heat Sinks
Heat sinks come in various shapes and sizes, each tailored to specific applications. Some common types include:
- Active Heat Sinks: These heat sinks incorporate fans or blowers to actively move air across the fins, increasing heat dissipation.
- Passive Heat Sinks: These heat sinks rely solely on natural convection for heat dissipation and do not include any integrated fans.
- Extruded Heat Sinks: Extruded heat sinks are created by forcing heated aluminum through a mold to create intricate fin patterns. They are cost-effective and find applications in many electronic devices.
- Bonded Fin Heat Sinks: Bonded fin heat sinks feature fins that are physically attached to the base using methods like brazing or welding. This type offers excellent thermal performance but can be more expensive.
- Pin Fin Heat Sinks: These heat sinks feature thin, cylindrical pins that extend from the base. They are suitable for applications with limited space and restricted airflow.
- Liquid-Cooled Heat Sinks: In some high-performance applications, heat sinks are combined with liquid cooling systems. These systems use a liquid coolant to carry heat away from the base plate, offering enhanced cooling capabilities.
Factors Affecting Heat Sink Performance
Several factors influence the overall performance of a heat sink:
- Thermal Conductivity: The base plate’s material determines its thermal conductivity, affecting how efficiently heat is transferred from the component to the heat sink.
- Fin Design: The arrangement, thickness, and spacing of the fins impact the surface area available for heat dissipation.
- Airflow: Proper airflow is essential for effective convective heat transfer. Higher airflow rates lead to more efficient cooling.
- Temperature Difference: The greater the temperature difference between the component and the environment, the more heat will be transferred.
- Surface Area: A larger surface area allows for more efficient heat dissipation.
- Mounting: Proper attachment using thermal paste or thermal pads ensures good thermal contact between the component and machining heat sink.
Real-World Applications
Heat sinks are present in a wide range of electronic devices, from smartphones to industrial machinery. Some notable applications include:
- Computers: CPUs heatsink and GPUs in computers require efficient heat sinks to maintain optimal performance and prevent overheating.
- LED Lighting: High-power LED lights generate significant heat. Heat sinks help dissipate this heat, preventing damage to the LEDs.
- Automotive Electronics: Heat sinks are used in vehicle components like power electronics and engine control units to manage heat generated during operation.
- Power Amplifiers: High-power audio and radio frequency amplifiers require heat sinks to prevent overheating and distortion.
- Solar Inverters: In solar energy systems, heat sinks are used in inverters to manage the heat generated during the conversion of DC to AC power.
Advanced Cooling Technologies
As technology advances, so does the field of thermal management. Engineers are continually developing innovative cooling solutions to address the heat challenges of cutting-edge electronics. Some of these technologies include:
- Vapor Chamber Cooling: Vapor chambers are flat, sealed containers filled with a small amount of working fluid. They efficiently spread heat in two dimensions, providing more uniform cooling.
- Phase Change Materials: These materials change phase from solid to liquid as they absorb heat. They can be incorporated into heat sinks to absorb and release heat during operation.
- Graphene-Based Heat Sinks: Graphene’s exceptional thermal conductivity makes it a promising material for heat sink applications, enabling more efficient heat transfer.
Conclusion
In the world of electronics, managing heat is crucial to maintaining optimal performance and reliability. Heat sinks play a pivotal role in this endeavor, providing a pathway for excess heat to escape from electronic components. Through the principles of conduction, convection, and careful design, heat sinks contribute to the advancement of technology by enabling devices to operate efficiently even under high thermal loads. As technology continues to evolve, the science behind heat sinks remains a cornerstone of modern electronic engineering, ensuring that our devices keep their cool and perform at their best.