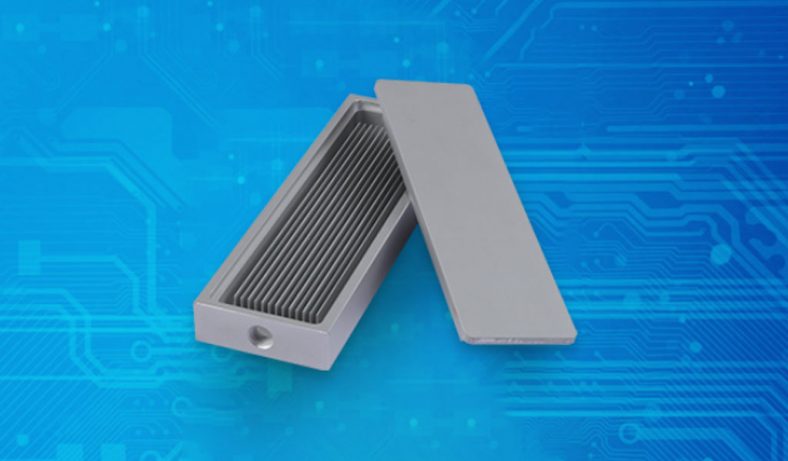
China Friction Welding Heatsink Specialist
Friction welding (friction stir welding) refers to the use of the heat generated by the friction between the high-speed rotating welding tool and the workpiece to partially plasticize the material to be welded. Under the action of rotational friction, it flows from the front of the welding tool to the rear, and forms a dense solid-phase weld under the extrusion of the welding tool.
With its high-quality, high-efficiency, energy-saving, and pollution-free technical characteristics, friction welding (friction stir welding) has been widely used in new technologies and traditional industries such as aviation, aerospace, nuclear energy, weapons, automobiles, electric power, marine development, and machinery manufacturing. more and more applications.
Friction welding heatsink is a kind of heat sink manufacturing process.Wonder often uses this process to make high-power heatsink. Compared with the traditional aluminum extrusion heatsink, the friction welding heatsink has a large size and a high height. density, high power and other advantages. Wonder can also use this friction welding process to achieve medium-free thermal fusion, and splicing two or more profiles to meet the needs of different shapes.
The Molding Step Of Friction Welding Heatsink
The Case Studies Of Friction Welding Heatsink
Our value is using faster time to fabricating the customer’s product, and help them to forward the product into market, This is also our target. Our advantage is one-stop shop service and faster manufacture time.
Lithium-battery-liquid-cooling-heat-sink High-power-air-cooled-liquid-cooled-radiator High-power-air-cooled-liquid-cooled-radiator Friction-stir-welding-heat-sink Friction-Solder-Cooling-Heatsink Laser Fiber Water Cooling Plate
The Advantages Of Friction Welding Heatsink
- The microstructure change of the heat-affected zone of the welded joint is small. The residual stress is relatively low, and the welding workpiece is not easily deformed;
- It can complete the welding of long welds, large sections and different positions at one time. Connector height:
- The operation process is convenient to realize mechanization and automation, the equipment is simple, the energy consumption is low, the efficiency is high, and the requirements for the working environment are low:
- No need to add welding wire, no need to remove oxide film before welding when welding aluminum alloy, no need for shielding gas, and low cost;
- Materials that are sensitive to thermal cracks can be welded, suitable for welding dissimilar materials:
- The welding process is safe, pollution-free, smoke-free, and radiation-free.